The meat industry covers both slaughterhouses and cutting plants as well as meat product (fresh, cured, or cooked) manufacturing plants. However, these are generally separated into slaughterhouse/cutting plant and manufacturing plant. Thus, whereas the former produce carcasses, half carcasses, meat cuts for consumption, the meat products industry produces transformed meat products (seasoned and cured meats, hams, sausages, etc.).
From an environmental viewpoint, the production of wastewater differs markedly depending on the type of installation concerned. Thus, whereas slaughterhouses/cutting plants generate large volumes of wastewater with a high organic load, production at manufacturing plants is lower and tends to remain fairly constant over time.
As described below, the majority of processes performed sequentially in a slaughterhouse generate wastewater:
- Delivery of the live animals/stabling: the animals arrive at the installation and are stabled. The wastewater produced when cleaning these zones contains urine, feces, hair, disinfectant, etc.
- Slaughter: the animals are washed externally using pressurized jets of water and then slaughtered. Wastewater is also generated during this process.
- Exsanguination: the animals are exsanguinated. The blood is collected for sale, although some spillage, which passes into wastewater upon cleaning, usually occurs.
From this point the subsequent processes vary between cattle and pigs. For pigs, these processes are as follows:
- Scalding: impurities are removed from the skin by immersing the carcass in boiling water. Wastewater is also generated during this process.
- Singeing: any hair remaining after scalding is removed using burners.
- Washing: the carcass is washed with pressurized water to remove any residues left after singeing. Wastewater is also generated during this process.
For cattle, the following processes are performed after exsanguination:
- Skinning: the skin, legs, and horns are removed from the carcass.
Cattle and pig carcasses then undergo a common series of processes:
- Conditioning: remnants such as entrails, from which by-products for animal feed are obtained, are removed. Wastewater is also generated during this process.
- Airing, butchering, and sale: the carcasses are cooled to room temperature, butchered, and moved to the end-product chambers ready for sale.
The processes for poultry are similar but with the difference that much more wastewater is generated during stabling and an intermediate defeathering process is included between the scalding and singeing processes.
As can be seen, wastewater is generated during almost all the processes involved as well as when cleaning the installations. The final volume produced is high and it has been estimated that around 5 liters of water is required per kilogram body weight for the live animal. Water consumption for poultry is higher at between 5 and 10 liters of water per kilogram of live animal. The wastewater generated generally carries with it slurries, meat remnants, blood, hair, pieces of entrails, and surface fat, which together mean that the water has a content of organic matter, material in suspension, oils and fats, nitrogen (ammonia and organic), phosphates, and detergents and disinfectants used during cleaning. In addition, the load in the wastewater varies markedly depending on the time of day and even from one hour to the next.
Typical values for the parameters related to the organic matter and nutrient content of the effluent generated in a slaughterhouse with cutting plant can be found in the following table.
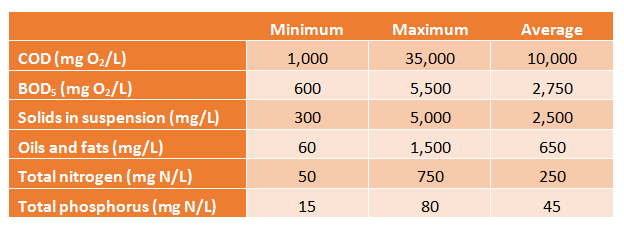
The most recommended option for treating this wastewater in an appropriate manner is a design that includes pretreatment of the water, which removes larger and smaller solids while also removing oils and fats and attenuating the fluctuations in flow and/or load, followed by a biological treatment to remove the organic matter and nitrogen. These steps are described in greater detail below:
- Pretreatment: the first process required involves the removal of larger and smaller solids using sieves with pore sizes of 10 mm and 4 mm, respectively. It is also advisable to separate oils and fats from the water prior to biological treatment due to their high oxygen demand. Flotation is an effective means of achieving this. finally, as a result of the fluctuations in flow and contaminant load during the productive cycle, it is advisable to include a flow homogenization and lamination step to attenuate the peaks that may occur over time.
- Biological treatment: this can be performed using several very different technologies, the most favorable of which are:
- Low-loaded activated sludges: it is possible to remove dissolved organic matter and achieve denitrification using a low-loaded biomass in suspension process in which the diffuser grid for the aeration system does not occupy all the bioreactor. Aerobic and anoxic regions are established in the reactor depending on the arrangement of the air diffusers, and their alternation allows nitrogen to be removed.
- SBR: a sequential discontinuous process can be used to remove both organic matter and nutrients. In the case of an SBR, all processes take place in the same reactor but sequentially in time. In order to work discontinuously, it is essential to have a tank in which the wastewater that passes into the treatment system can be stored.
- Anaerobic process: both organic matter and nitrogen can be removed from the wastewater by way of an anaerobic treatment that does not require oxygen. As a product of the sequence of transformations that occur during the process, some of the carbon in the wastewater is transformed into biogas, a revalorizable mixture of carbon dioxide and methane.
The three biological treatments mentioned above are efficient and robust, and each has its own advantages and drawbacks. However, it should be noted that the anaerobic biological treatment option results in lower operating costs due to its lower energy consumption while also generating biogas.
In summary, slaughterhouses/cutting plants generate large quantities of effluents with a high organic load (dissolved and in suspension) in addition to containing nitrogen, phosphorus, oils and fats, and pathogens. The most recommended treatment system is based on the design of a complete system involving water pretreatment to remove large and small solids, along with oils and fats, and a biological treatment that removes the organic load and nutrients from the water. If the biological treatment is anaerobic, the biogas generated can be used to produce electrical energy, thereby reducing the overall consumption of the installation.